Lean to be 'GREEN'
- Kathleen Lausman
- Oct 20, 2016
- 5 min read
Canadians have been pursuing sustainability in the building industry for some time. Many building projects target a level of Leadership in Energy and Environmental Design (LEED) using the rating system devised by the United States Green Building Council (USGBC) to evaluate the environmental performance of a completed building.
What is ‘Green’ or Sustainable?
One definition offered by the Global Development Research Center (GDRC) is "Green or sustainable building is the practice of creating healthier and more resource efficient models of construction, renovation, operation, maintenance and demolition." The simplest and most fundamental definition is "the ability to sustain" or " capacity to endure".
But, what about sustainable processes in designing and constructing a building? How sustainable are traditional design and construction practices?
Research has indicated construction productivity vs other major industry productivity (non-farm) over the past decades 1964 - 2012 has been static or actually in decline.
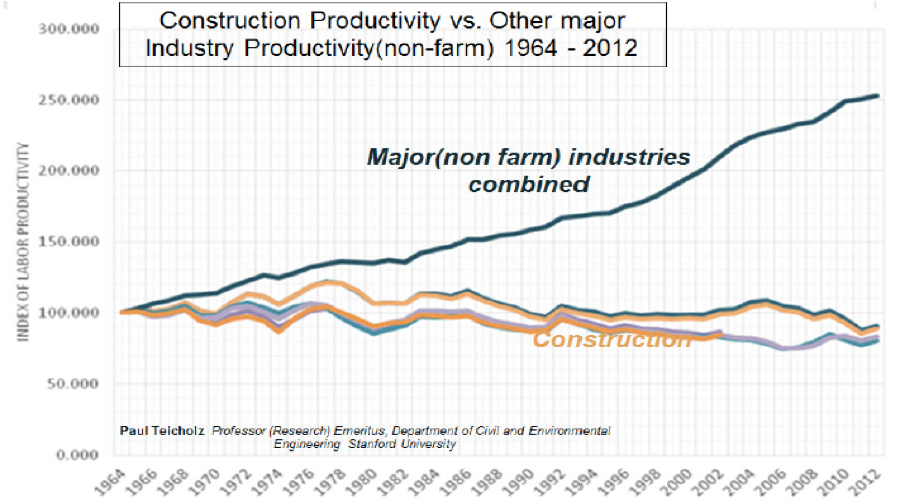
Figure 1:Paul Telcholz Professor (Research) Emeritus, Department of Civil and Environmental Engineering, Stanford University
Owners continue to be dissatisfied with this performance. Seventy (70%) of projects are delivered over budget, miss the completion date, are difficult to maintain once in use and may not deliver on desired sustainability targets over the facility service life.
Traditional design and construction practices are wasteful and fall short on value to the Owner.Avoidable wastes equate to 50-65% of a traditional project cost while another 25-35% is unavoidable waste inherent in processes that are required to support design and construction such as accounting. By contrast, the actual value produced in a traditional design and construction project is a mere 10%.
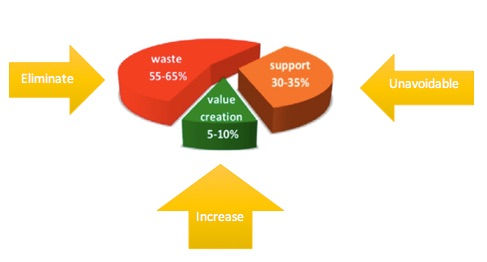
Figure 2: Waste in Building Industry
In short, creating waste is not a sustainable practice.
The good news is the building industry is improving through Lean Project Delivery principles and methods. Lean Project Delivery is based on the Toyota system used in manufacturing.
While Lean Project Delivery has been in practice in the US and a number of European countries for the past two decades, it is a relatively new practice in Canada that is showing impressive results toward sustainability - increasing value through waste reduction or elimination.
Lean design and construction methodology works to minimize the waste of materials and labour efforts resulting in the generation of greater value. The most effective ways to satisfy Owner requirements define value.
“Norman is Broken. There is a better way,” says Dennis Cuku, owner and visionary for the Mosaic Centre.
Projects like the Mosaic Center in Edmonton, Alberta have achieved high sustainability targets in both the processes of project delivery and the resultant facility performance through the Lean Project Delivery approach. The five main Lean principles applied on this project: indentify value; map the value stream; create flow; establish pull; and seek perfection. Lean methodologies reduced waste, increased value and delivered a 'net zero' energy facility three months ahead of schedule and 3% under budget!
The Mosaic Centre is the first triple bottom line commercial building incorporating three dimensions of an organization’s performance: social, environmental and financial.
[Review details of this Lean Integrated Project Delivery at www.themosaiccentre.ca.]
In most traditional building projects, facility commissioning is often an after-thought or employed at construction substantial completion as an inspection process on HVAC and electrical systems. Construction 'punch lists' are lengthy and can take years after the facility is occupied to get resolution. Outstanding "as-built" drawings and Operation & Maintenance manuals, outstanding paperwork for LEED designation, HVAC balancing issues, are typically the norm. Why is this the case? After the new facility ribbon cutting and speeches, the project team is well on its way to the next project. The Owner facility manager is the last one standing and likely the least involved with the project delivery processes.
With Lean projects, "Done is Done" cites Murray Guy of Integrated Designs Inc. In Lean projects both the commissioning agent and facility manager become part of the project delivery team from design to building turnover. "No outstanding deficiencies that take years to address." says Murray Guy, an early adapter of 'Lean to be Green' who has worked on a number of projects that deployed Lean methodologies to meet high building performance sustainability targets.
Three recent Lean Project Delivery projects with high sustainability targets include The Mosaic Centre in Edmonton, Okanagan College Trade Centre in Kelowna and the Richardson College for the Environment at the University of Winnipeg.
The enduring sustainability aspects of Lean Project Delivery are the principles that support the practice as articulated in the book "The Toyota Way, 14 Management Practices" by Jeffery K. Liker. These principles support the triple bottom line of sustainability - Environment, Social and Economic.
For the facility Owner, what does this mean?
Lower project cost, better schedule, and better quality - not a trade off between all three. This is achieved using Lean Project Delivery. Continuously learning how to design and build more energy efficient structures using less wasteful processes to directly support Owner business goals.
For the project designers, constructors and supply chain, what does this mean?
More efficient productivity, less risk contingency, less waste, greater safety, less adversary, greater learning, better relationships and above all – greater profitability. This level of performance on projects also results in a sustained competitive advantage and economics.
A common Facility Manager adage suggests the most energy efficient buildings are the ones not occupied. Clearly, the purpose of buildings are to support the work activities of the occupants. While Energy Modeling and the tools that support predicting energy performance in a building are critical, modeling 'future state' - (how work activities can be more efficient in a new facility) as opposed to 'current state' (how work activities are currently completed) is enabled with Value Stream Mapping (VSM) of building occupant work activities, then modeling and prototyping design solutions to best support this value within a new facility. These methods were critical to the Moose Jaw hospital project enabling the project team to work with the user groups to map the future state work flow processes reducing waste of time, space, energy and more responsive customer service.
Lean projects use Target Value Design (TVD), the Last Planner System®, Choosing By Advantage and other methodologies where architects, engineers, constructors, major trades, the estimator and the Owner facility manager collaborate, really collaborate together in the same room to understand problems; then design solutions that are within the construction budget and construction schedule and deliver high performance and lower cost buildings over the facility life cycle. These methods are both Lean Project Delivery and sustainable practices.
Impossible some say!
The ‘proof is in the Lean Project pudding’. Much research has been completed and data continues to be gathered on Lean Project Delivery as part of the continuous learning Lean principle. The research results are astounding in improved performance as reported by building industry Lean practitioners.
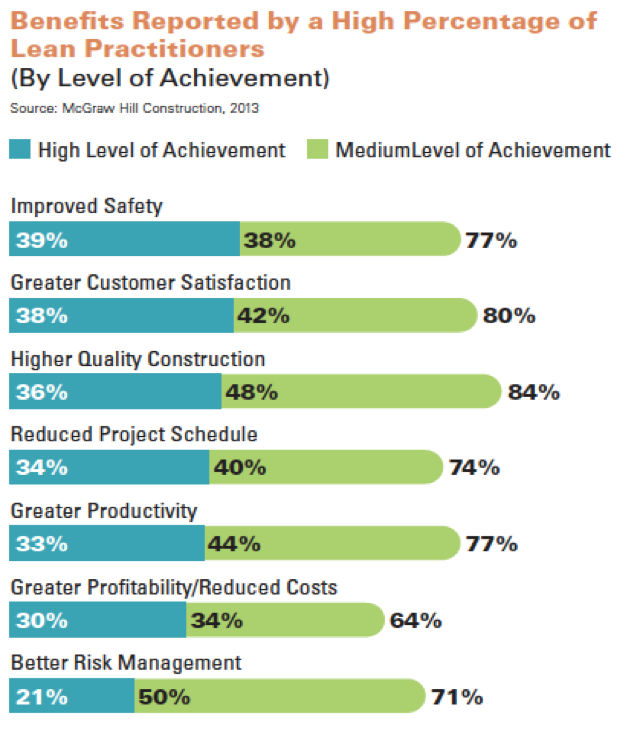
Figure 3: McGraw Hill Construction, 2013
As the Federal and Provincial governments continue to focus on sustainability and ‘green’ infrastructure, Lean Project Delivery offers significant opportunity to deliver impressive, more sustainable results. Lean improves productivity in design and construction processes and delivers on triple bottom line sustainability targets.
The Lean Construction Institute – Canada (LCI-C), a non-profit special committee of the Canadian Construction Association (CCA) is focused on improving the building industry performance through awareness, education and training in Lean Project Delivery. Lean methodologies are applied to many different project types and are used in conjunction with all existing project delivery models. Visit www.lcicanada.ca for additional information on becoming “Lean to be Green”. Projects are collaborative efforts that succeed when Owners, Designers, Constructors, Major trades and their supply chains work together.
Projects are collaborative efforts that succeed when Owners, Designers, Constructors, Major Trades and their supply chains work together in the same room on the same problems at the same time.
Be Lean to be Green!
Comments