Yet another Foreigner that does not understand LEAN
- Murray Guy
- Mar 10, 2016
- 3 min read
A Lean Story
Niklas Modig a researcher at the Stockholm School of Economics went to Japan to learn how lean philosophies can be applied to non manufacturing business operations and was fortunate to be able to spend spend thousands of hours inside Toyota’s service organizations.

On one of the first visits, Niklas was greeted by Nishida-san one one of the youngest senior managers at Toyota, and asked why are you here? Niklas responded that he carried out research in lean services and wanted to know how to apply lean practices to lean service companies.
Nishida responded “Yet another foreigner who does not understand anything.” You have just asked a question that shows, you do not understand what the Toyota Production System is all about. If you are going to be here for two years, I recommend that you try to understand our core philosophy. Our values and principles, guide everything that we do.

Niklas, at Toyota we consider our customers as a beautiful tree. All of our decisions are strategic in that we want the tree to be more beautiful, healthy and growing. It is our commitment to always focus on the customer, that enables Toyota be successful.
We have discovered that there are two main principles that enable us to provide value for our customers. The first principle is called Just–in-Time. This is the principle of how we make decisions about work FLOW. Think of it as playing a football game where our team passes the ball down the field, kicking it back and forth taking a perfect path. The ball flows down the field and into the goal representing delivery of exactly what the customer wants, on time and only the quantity needed to meet the demand.

The second principle is JIDOKA, is a little harder to understand as it is more abstract. JIDOKA is when all the players understand the rules and the team’s strategy for winning games. For this to occur all players must be able to see the scoreboard, see all the other players, hear the crowd, team and the referee’s whistle.
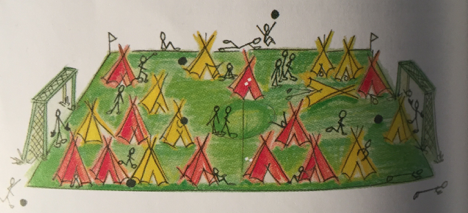
In most organizations the field looks dis-integrated with people and teams working in silos kicking their own balls around and not paying attention to focusing on the customer and scoring goals.JIDOKA then is about creating a visible and clear picture so that if anything disturbs flow it can be identified and fixed immediately.

Employee engagement from the bottom up is key streamlining processes that is why we empower our people to take time-outs to stop production to solve problems so that we continually improve the process.
In addition to focusing on the customer, creating flow and stopping to fix problems there are a number of methods that contribute to our success. We standardize processes so everyone has the same understanding of how to complete a task. We use visual planning so that everyone can see the work and progress. We also use tools like rolling whiteboards with production schedules and activities like stand-up meetings to implement the production system. We need to understand and pay attention to the word SYSTEM as this means that everything in connected.
So at TOYOTA we understand lean as an Integrated System as opposed to a collection of methods and tools.

Lean Principles and Practices Summary To help make the Toyota Production System clear Nishida-san wrote on the whiteboard!
Value defines how an organization should behave
Principles define how an organization thinks
Methods define what an organization should do
Tools define what an organization should have
When we build an organization with a lean SYSTEM we reduce the variation in the way people behave, think and act. This helps to achieve consistency in delivering the VALUE desired by the customer.
Murray Guy @Lean_tobe_Green
mguy@i-designs.ca
For more information on Lean Project Delivery, you can arrange for a work shop or take a course at LEAN LAB . If you would like help implementing lean on your project, Integrated Designs can join your team as a facilitator.
Comments