Target Value Design | An Assessment of the RCFE Project
- Murray Guy
- Mar 2, 2016
- 5 min read

The Richardson College for the Environment project got into budget issues when project's Big Dream could not fit in the not so BIG budget. The financial reality was that there was $38.5M and not $50M that was estimated for the initial design concept.
The team were then tasked with finding over $10M in our "Broken Buildings Busted Budget" reality. It just so happens that this book helped to convince the U of W to adopt a Lean Project Delivery approach, for this project.
Our team was successful in delivering this project. To see how we faired , we are going to compare our approach to Target Value Design best practices outlined in an article by Glenn Ballard.
Glenn Ballard (2011) Target Value Design: Current Benchmark. Lean Construction Journal 2011 pp 79-84 www.leanconstructionjournal.org
Introduction
The University of California, Berkeley’s Project Production Systems Laboratory periodically publishes a description of the current benchmark in each project management process that is a subject of research.
In the building sector, it has been customary for architects to work with customers to understand what they want, then produce facility designs intended to deliver what’s wanted. The cost of those designs has then been estimated, and too often, found to be greater than the customer is willing or able to bear, requiring designs to be revised, then recosted, and so on. This cycle of design-estimate-rework is wasteful and reduces the value customers get for their money. Cost has been an outcome of design.
The following is an assessment of the process based upon this paper
Some of the project constraints that were non-negotiable were that this needed to be a signature high performance sustainable building, incorporate three science departments and meet the needs of a tight budget with high expectations on value and an aggressive schedule. Ideally the feasibility of the project is determined early in the project, ours was not. We needed to fix a budget with a project on the critical path to a two-year occupancy, with no design to meet budget. This was our challenge!
Once we had all of the key trades on board we rolled up our sleeves, set the target, defined the constraints and prioritized what represented value for the U of W stakeholder group. There needed to be an understanding and commitment to the budget as there was no pot of Gold at the end of the design process to top up any budget gap.
NO MORE MONEY | No Hidden Contingency to Save the Day
At the bi-weekly all hands on deck sessions our project team groups needed to report in to the master Target Value Design spreadsheet with the cost saving measures identified as priorities for hitting target cost. To save time we used “Cowboy Math” to quickly determine the feasibility of any proposed measure. This helped to minimize design and costing time.
Although we did not formally know about the Last Planner System or Pull Planning, our team leader Bill Sharpe pulled the necessary information from the TVD cross-functional teams working on the over 100 value management IDEAS on the table at any one time. At each bi-weekly meeting where we would get the whole team together in a large conference room (Big Room) we would update the project cost estimate to reflect the current estimates and value management opportunities. This was a plus/minus report as sometimes the Owner’s Project Requirement would change with new programming requirements.
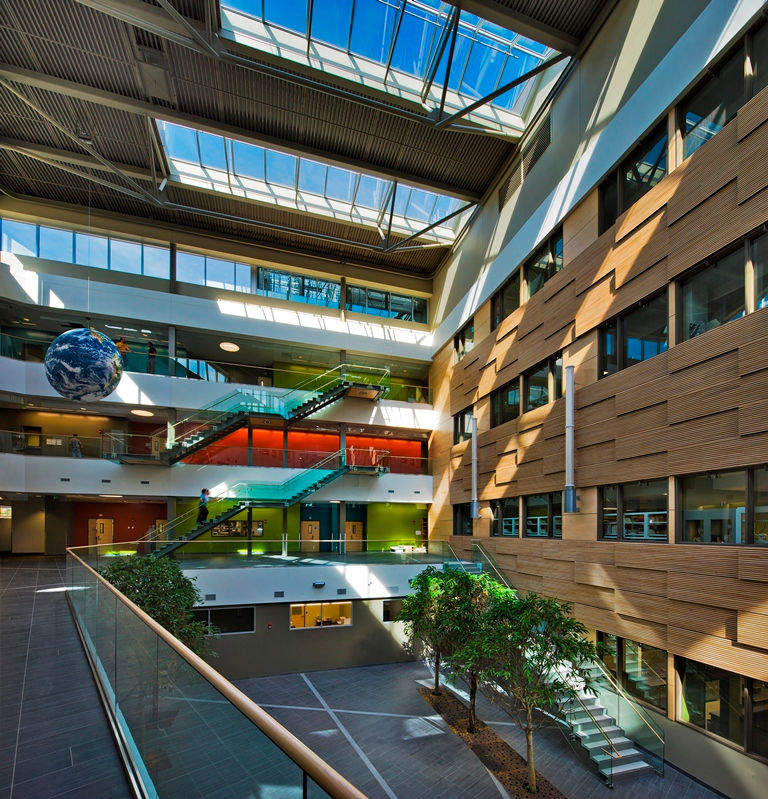
Our team did not co-locate as is common with many teams facing challenging work, however one would need to understand the culture of Winnipeg in that it acts and feels like a small market business is based upon RELATIONSHIPS. With strong relationships and high expectations for deliverables it could be argued that this project was dynamic co-location as the work got done, the conversations were almost daily and we pinned the tail on the donkey.
Did we meet success criteria for Effective TVD? (Yes to all of these)
Clear understanding of customer value.
Consolidated reporting and deliverables at greater intervals.
Co-location or some form of it is desirable for challenging projects requiring focused work
Key members of the project team are selected through value based proposals
All team members have an equal say at the dinner table, no exceptions
Solutions are developed with cost, schedule, and constructability as criteria
Work is completed in smaller batches
Team members are aligned with pursuit of project objectives.
Did we have the right Attitude and Behavior changes required? (Yes to all of these)
Standard processes to encourage collaboration
Inclusion of all team members
Empowering and requiring team members to declare breakdowns
Education, coaching and building trust among team members
Commitment to the fact there is no more money or extras other than a real small CONTINGENCY
Did we incorporate some more advanced methods and procedures? (Yes to these)
Management of individual team member contingency will improve
Reduction of contingency in estimates
Proactive value engineering
Did we incorporate some more advanced methods and procedures? (Room for Improvement on these)
Adoption of more collaborative information technologies
Ability to target an expected cost saving which is currently between 10% to 40%
Better alignment of team member interests
Minimum viable product strategies
Ability to delay decisions to the last possible moment through set based design
Choosing by advantages for better decisions based upon customer value
A3 business planning and team selection
Whole life investment decision
Lean teams will self assemble and be way more competitive
Stakeholder value will be more clearly defined early enabling better scope control
We will reduce the number of stakeholder with more integrated practice
How did we do?
Target Value Design enabled the RCFE team to fix a BIG Dream project on a Smaller Dream budget and deliver an exceptional project that did achieve the project requirements within amazingly tight time and budget constraints. The team needed to get started with shoring and foundations before the project was designed, deliver a $43.8M 70% laboratory building project with 65 fume hoods, vivarium, green house with only a $750,000 contingency.

Contingency management was key in holding the team accounable. What was achieved is amazing considering that $450,000 of the contingency was used on one code related issue that emerged on an interpretation of stairwell pressurization to meet fire code.
With regards to sustainable performance which was a top priority, our team exceeded the LEED Silver requirements, Got Gold and through Innovation and Imagination in Laboratory design delivered one of North America's most energy efficient laboratory projects at 58% less energy that MNECB.
Upon review of the TVD process, our team did pretty darn good!
Comments